Home > 3D Tracking – Enabling Precision Navigation for OEMs
3D Tracking – Enabling Precision Navigation for OEMs
Much like vehicle GPS navigation, coordinate data are used to show where an object is in 3D space, and where it needs to go next. With vehicle GPS navigation, the car is moving and the destination is fixed. A map supplies the travel route. However, only a 2D (planar) view of the vehicle’s position is available, and only movement along the longitude and latitude lines (X and Y axes, respectively) is shown. Altitude info (Z-axis) is missing, as is rotational data – only two degrees-of-freedom are reported. A view that limited cannot support complex OEM surgical navigation applications
The Polaris® optical measurement solution, and Aurora® and 3D Guidance® electromagnetic (EM) tracking solutions capture the position (X-Y-Z coordinate data) and orientation (roll, pitch, yaw) of an optical navigation marker or EM sensor in relation to a fixed object or reference point in 3D space.
Position and orientation measurements also refer to the “degrees of freedom” (DOF) in which an object moves in 3D space. There are six degrees of freedom in total; NDI’s solutions capture all six degrees of freedom in real-time. This type of technology, known as 3D measurement, spatial measurement, or 3D motion tracking, can be used for real-time tool tracking and navigation purposes.
Motion Tracking in All Directions
3D tracking technology provides that needed detailed view by digitizing, formatting, and enabling visualization measurement data. Positional movement of the optical navigation marker or EM sensor can be tracked on the X, Y and Z axes of a 3D coordinate system. Rotation (roll, pitch and yaw) on these axes is calculated as orientation data. Movement in all directions is known, from any angle/perspective. This movement is reported in relation to a fixed object or reference frame; i.e., a ‘home’ location. Multiple objects—and their respective locations to each other—can be dynamically tracked at once.
To apply the GPS analogy to surgical navigation applications, patient imaging datasets represent the map. The target/treatment site is the destination. And an EM sensor embedded into an OEM surgical instrument such as a catheter, or a medical instrument fitted with optical markers act as the vehicle.
3D tracking technology can enable the position and orientation of the catheter or instrument to be known in relation to its home/start location and destination as it’s navigated through the body. The catheter or instrument’s path (route) is visualized, planned, navigated, and presented in real-time to the clinician in the host OEM software interface.
3D tracking technology bridges the gap between static patient images and dynamic instrument movements; it brings the physical world into digital interfaces. The live stream of measurement data allows instruments to be shown at the right place, at the right time. As with GPS navigation, the value of 3D tracking technology is tied to its accuracy. It’s the difference between arriving exactly at your destination or being off by miles – or millimetres in surgical navigation applications.
Related Articles:
5/6DOF Sensors: Enhancing Medical Instrument Navigation
Why Accuracy Matters: Precision in OEM Surgical Navigation
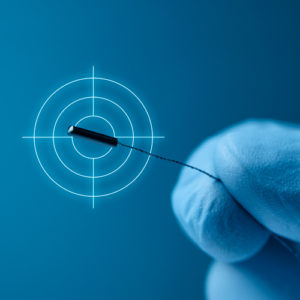
Why Accuracy Matters
Learn about the importance of accuracy in optical measurement and electromagnetic tracking.
Legal Disclaimer
NDI tracking and measurement products are general metrology components that can be integrated into customer products, research experiments, and/or as components of medical devices that require precision measurement and tracking. While NDI components and technology can be integrated into original equipment manufacturer (OEM) medical devices, they are not specifically intended for a given application and, as such, have not been developed or manufactured in accordance with medical device standards. It remains the responsibility of the OEM customer or end-user to determine and test the suitability of NDI components and technology for their intended use, including performing any required ethics approval, verification, and validation required to demonstrate suitability and compliance. System-level testing, certification, and validation are the responsibility of the original equipment manufacturer or the applicable end-user and should be completed prior to the use of NDI products or technologies in any application.