3D Guidance® Sensors
3D Guidance® Sensors Five different 6DOF sensor options support flexible integration into numerous OEM instruments and tracking applications.
Sensors Come Fully Assembled and Ready for Use
3D Guidance® sensors come in many sizes, from a larger reference sensor that consists of an 8 mm square cross-section, to a 0.56 mm diameter cylindrical sensor for use in the smallest tools. The sensors can be integrated into diverse OEM medical instruments such as ultrasound probes, catheters, epidural and biopsy needles, and more. Only 6DOF sensors are available; however, they are re-usable.
The 3D Guidance electronics unit can simultaneously track up to four sensors and supports interchangeable sensor sizes. 3D Guidance sensors come pre-wired with connectors and pre-characterized for immediate use; no assembly is required.
With the 3D Guidance solution, the sensor dictates the size of the measurement volume, whereby the larger the sensor, the larger the measurement volume. (This differs from our Aurora solution, in which the field generator determines the size of the measurement volume.) The 3D Guidance solution maintains a standard positional accuracy of 1.4 mm RMS and orientation 0.5° RMS, regardless of the sensor or transmitter that is used.
3D Guidance 6DOF Sensors
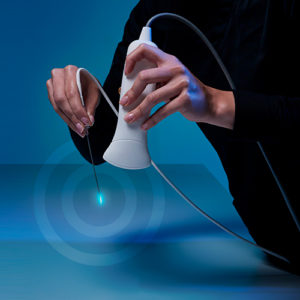
Learn how Sensors work as part of Electromagnetic Tracking Technology
Download our 12-page Education Guide to learn how you can integrate Electromagnetic Tracking Technology into your OEM medical devices to:
- Navigate instruments safely and reliably through complex anatomy.
- Target small treatment areas with
sub-millimeter accuracy and precision. - Visualize real-time position as well as orientation of an instrument.
- Track instruments even when they
are out of sight. - Embed micro sensors into flexible and
rigid instruments.
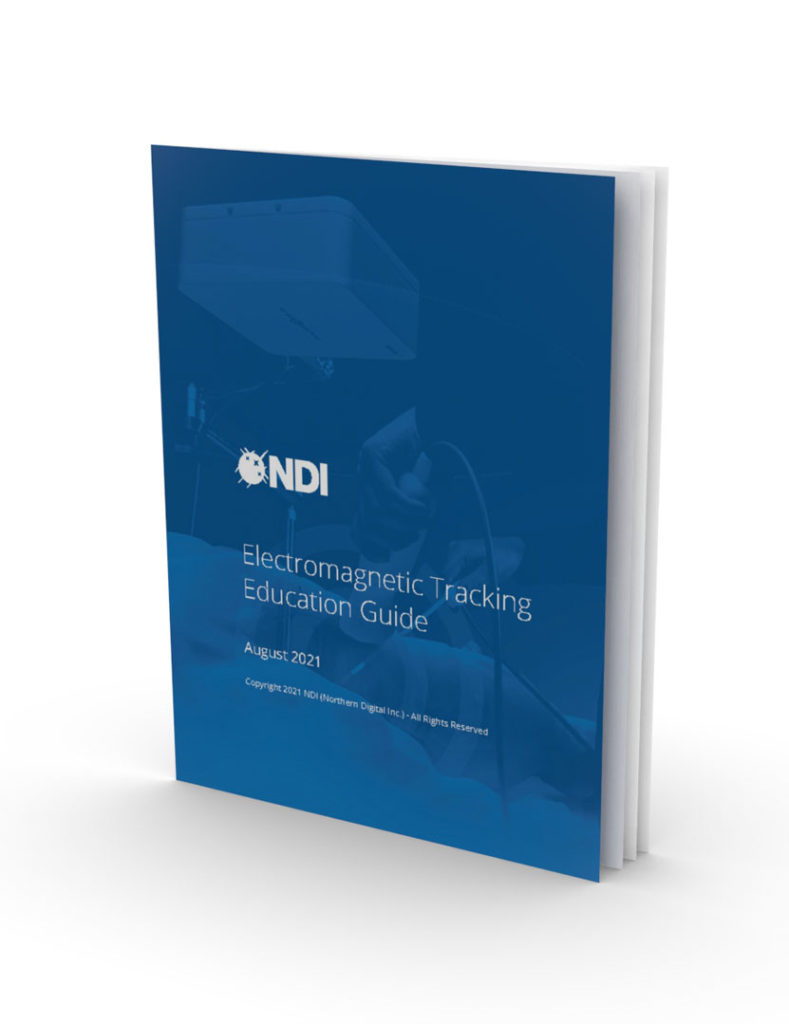
Legal Disclaimer
NDI tracking and measurement products are general metrology components that can be integrated into customer products, research experiments, and/or as components of medical devices that require precision measurement and tracking. While NDI components and technology can be integrated into original equipment manufacturer (OEM) medical devices, they are not specifically intended for a given application and, as such, have not been developed or manufactured in accordance with medical device standards. It remains the responsibility of the OEM customer or end-user to determine and test the suitability of NDI components and technology for their intended use, including performing any required ethics approval, verification, and validation required to demonstrate suitability and compliance. System-level testing, certification, and validation are the responsibility of the original equipment manufacturer or the applicable end-user and should be completed prior to the use of NDI products or technologies in any application.