Home > 5/6DOF Sensors: Enhancing Medical Instrument Navigation
Navigating 5DOF and 6DOF Sensors in Electromagnetic Image Guidance
As a global leader in electromagnetic (EM) navigation, one of NDI’s specialties is researching and designing 5 (Degrees of Freedom) DOF and 6DOF sensor technology used in EM tracking systems. The distinction between 5DOF and 6DOF sensors is critical to enhancing the accuracy and control of medical instrument navigation within the body.
In this article, we’ll explore the differences between these sensor types, situations that may require one over the other, and how our expert integration team supports customers with different sensors based on their unique medical device needs.
What are Degrees of Freedom and How Are They Reported?
Aurora® sensors are defined as either 5DOF or 6DOF, and 3D Guidance® sensors as 6DOF, where the degrees of freedom (DOF) describes the number of axes in which a rigid body (object) moves freely in 3D space.
Degrees of freedom are reported as translations and rotations.
Translations (positions) on the X, Y, and Z-axes correspond with the following motion:
- Moving forward/back on the X-axis (surge).
- Moving left/right on the Y-axis (heave).
- Moving up/down on the Z-axis (sway).
Rotation on these axes provides orientation data:
- Tilting side-to-side on the longitudinal/X- axis (roll).
- Tilting forward/back on the transverse/Y-axis (pitch).
- Turning left/right on the normal/Z-axis (yaw).
With 5DOF sensors, all three translations, and two of the three rotations are reported. Roll is excluded. Tracking in 5DOF could be based on movement limitations of the object, i.e., the object cannot physically turn (roll) side-to-side. Or it could be based on the object’s configuration and how it’s manually manipulated, such that its roll information does not need to be reported. For example, tracking the roll rotation of a needle is less important than knowing the position of the needle’s tip and the direction of where the tip is pointing. The roll orientation data is unnecessary.
With 6DOF sensors, all three translations and rotations are reported on the X-Y-Z axes. This means the ridged body, object, or system can move or rotate independently along all six possible axes in a 3D space. (It also means reporting an object’s roll movement is necessary during the navigated procedure.) This level of freedom allows for more complex movements and orientations to be tracked when navigating inside the body. Another example would be that a robotic arm with 6DOF can reach a wider range of positions and orientations compared to a system with fewer degrees of freedom.
How NDI’s Aurora and 3D Guidance EM Technology Obtain 6DOF Measurements
Due to their sensor designs, Aurora and 3D Guidance obtain 6DOF measurements by different methods.
For Aurora, two 5DOF sensors are fixed at an angle relative to each other to obtain the roll orientation data of a 6DOF sensor. During the characterization process, the two 5DOF sensors are combined into one single 6DOF sensor, with only the position and orientation measurements shown for the 6DOF sensor, not two sets of 5DOF measurements.
The Aurora calculates the tool’s transformation (position and orientation) relative to the field generator’s global coordinate system or relative to another 6DOF reference sensor affixed to the patient.
With the 3D Guidance, the design of the transmitter and sensor allows 6DOF values to be achieved using a single sensor.
Although the Aurora and 3D Guidance solutions take different approaches to 6DOF tracking, the result is the same: via embedded sensors, the OEM host application knows if the medical instrument is ‘facing the right direction’ or ‘right side up’ during navigation (or if it’s not). This is particularly important when tracking OEM medical instruments (such as scopes or catheters) that may roll or turn as they’re navigated through tortuous anatomical tracts.
Meeting Unique OEM Customer Needs With 5DOF and 6DOF Sensors
We understand that each customer’s medical device has unique tracking requirements as it relates to instrument size, where and how the instrument is navigated, and benefits for improving procedure efficacy and outcomes via navigation.
NDI has a full suite of standard 5DOF and 6DOF sensors, designed in-house by our expert sensor engineers, to support different tool and application integrations. Additionally, our integration team at NDI works with customers to identify and address the intricacies of new sensor integrations. For example, suppose a customer doesn’t have space inside their medical device to put a 6DOF sensor due to its larger size. In that case, as we have done with Aurora integrations, there’s the possibility of using two 5DOF sensors in their device, fixed relative to each other, to produce their own 6DOF sensor.
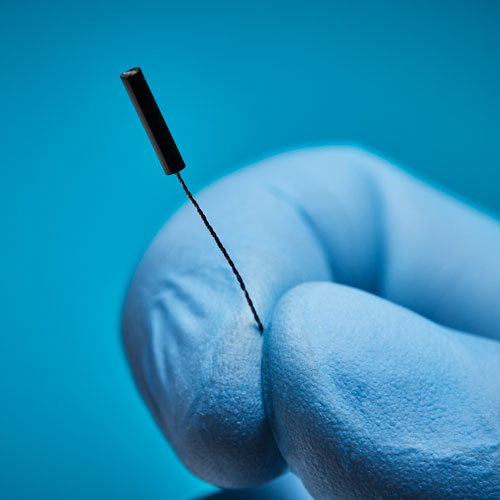
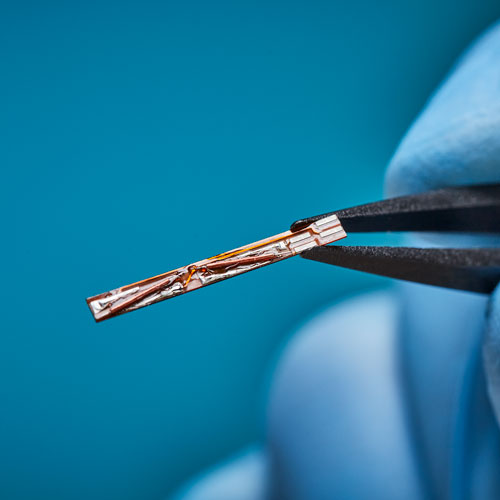
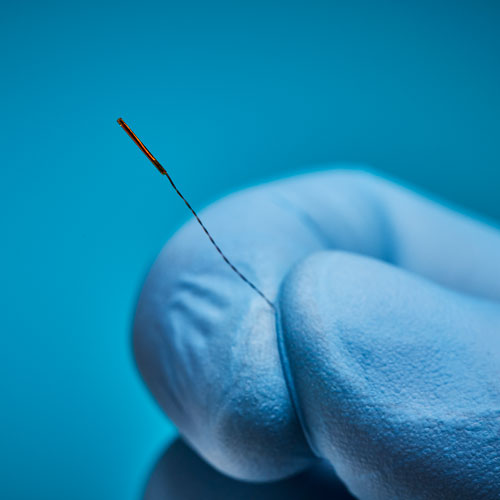
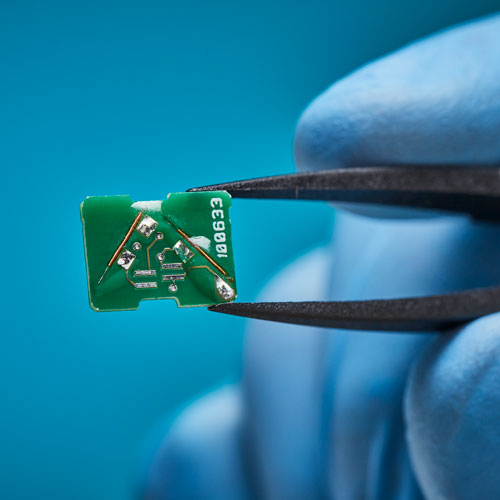
Aurora 5DOF and 6DOF Sensors
Are There Advantages of Using 5DOF Sensor Tracking?
In some applications, using 5DOF sensors for tracking can be sufficient because the practitioner doesn’t need to see the roll orientation data. For example, if a customer has a symmetrical device, the roll information doesn’t matter because it won’t provide any additional tracking information about the tool. In this case, customers can use a 5DOF sensor with all the benefits required for precise tracking.
The choice between 5DOF and 6DOF sensors is not merely technical; it’s a decision that shapes the landscape of medical interventions. With this comprehensive exploration, OEMs can approach sensor selection with a deeper understanding of each sensor type’s capabilities.
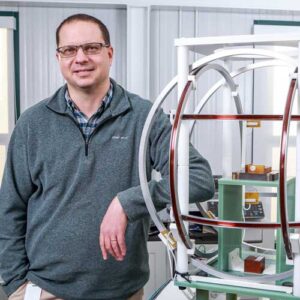